Optimal Designs for Unit-Load Warehouses
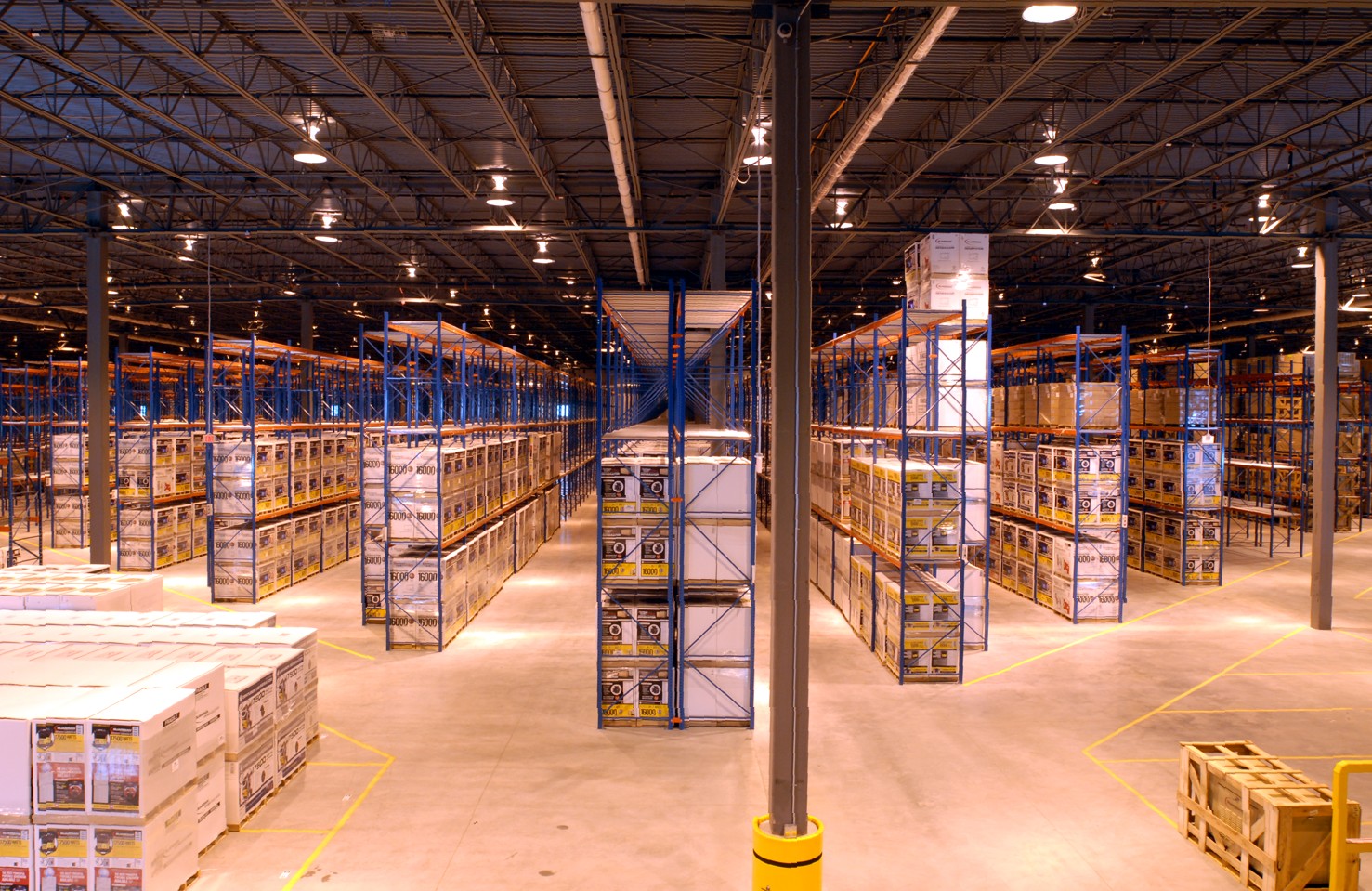
In a traditional warehouse, storage racks are arranged to create parallel picking aisles, perhaps with one or more cross aisles to allow workers to move quickly between picking aisles. This structure forces workers to travel rectilinear distances (north-south and east-west) to picking locations.
The traditional design is based on a number of unspoken, and unnecessary, assumptions. Why, for example, must cross aisles meet picking aisles at right angles? Or why do picking aisles have to be parallel? The answer, of course, is that they do not, and our research shows that adhering to these assumptions could result in a significant penalty in labor costs.
We consider the problem of arranging picking aisles and cross aisles in new ways to reduce the cost of travel within warehouses. Our models produce alternative designs that promise to reduce travel distances in a reasonably-sized warehouse by more than 20 percent (for some operations). Below is an example that maintains parallel picking aisles, but allows the cross aisle to take on a different shape. We call this the “Flying V”. If travel begins and ends at the bottom of the V, the expected distance to retrieve a single pallet is 10% less in this warehouse than in an equivalent traditional design.
Travel in a Flying-V is along 3 possible paths. Workers can–and should–travel rectilinear paths to locations near the bottom of warehouse; they use the cross aisle to access both locations above the cross aisle and locations slightly below it. Notice that travel to items below the cross aisle seems less efficient than to items above it. To address this, we relax a second unspoken assumption–that picking aisles must be parallel. We call this the fishbone design.
The Chevron design has a single, vertical cross aisle and picking aisles at angles 45 and 135 degrees. As with the Fishbone design, the idea is to allow workers to take “straight line paths” to locations as closely as possible.
The Leaf design is similar to the Fishbone in that it has two cross aisle segments, but we have relaxed the requirement that picking aisles be vertical or horizontal. Cross aisles in the Leaf design are steeper than in a Fishbone design, and picking aisles on the right and left sides are at an angle that reduces expected travel.
Notice that the Leaf requires more space around the pickup & deposit (P&D) point at the bottom, which is a disadvantage of the design because the otherwise best locations are displaced. This phenomenon is even more notable in the Butterfly:
So, there is a tradeoff: increasing the number of cross aisles makes travel nearer and nearer to direct “travel-by-flight,” but at the cost of displacing the locations nearest the P&D point. When is it no longer beneficial to add additional cross aisles?
Below is a plot that partially answers that question. The Chevron design has the lowest expected travel distance (highest percent improvement over a traditional design) when the number of aisles in an equivalent traditional design is 27 or fewer. For warehouses between 29 and 63 aisles, the Leaf design is slightly better than Chevron. For warehouses greater than 65 aisles, the Butterfly is ever-so slightly better than Leaf.
These observations lead us to conclude that for operations conforming to our main assumptions the Chevron is the best design for warehouses of realistic size.